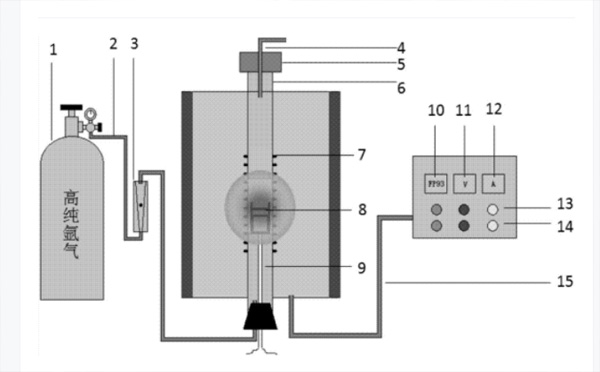
流化床气化炉因采用的原料多样化、炉内气氛复杂,对内衬耐火材料层存在侵蚀和破坏,内衬耐火材料衬里的使用寿命对气化炉长周期稳定运行影响巨大。气化炉内衬耐火材料的选取和烘制是关系到煤气化工艺成败的关键技术。本文对耐火材料的种类、性能要求及失效机理进行了介绍,并对流化床及耐碱腐蚀常用耐火材料的研究现状进行了综述,针对流化床煤气化工艺特点,提出了气化炉内衬耐火材料选取及内衬施工等的建议,为流化床工业炉内衬耐火材料的筛选及制作提供指导。
加压流化床煤气化技术是近年来随着洁净煤技术的兴起而发展起来的新一代大型、先进煤气化技术。通常高温高压的煤气化反应特点要求在气化炉内部必须加设耐火材料衬里。气化炉结构通常分为3层:最内层为直接接触高温介质的耐火材料层;中间层为保温材料层;最外层为不锈钢炉壳。除了反应器结构和附属设备等关键技术外,由于温度、压力及其它反应工况等条件的要求,其反应器衬里材料的选择和烘制也是关系到工艺成败的关键技术。内衬耐火材料衬里的使用寿命对气化炉长周期稳定运行影响巨大。
煤气化工艺因采用的煤种繁多、品质各异,流化床气化炉内反应工况复杂,通常伴有高温氧化、硫化、氢化、碳化、氯化等的气氛腐蚀,同时对于高碱金属煤种或添加碱金属催化剂的工艺还可能引入碱腐蚀等问题,该些侵蚀严重影响了耐火材料的使用寿命,并且对高温装置的安全稳定运行造成不良影响。气化炉内腐蚀的发生使得耐火材料的选择和使用寿命备受关注。
1、耐火材料的种类及失效机理
耐火材料依照不同的分类标准具有不同的分类。具体可以根据化学性质不同分为碱性、中性及酸性耐火材料;根据供货形态不同,分为定型耐火材料与不定型耐火材料;根据是否经过烧制,分为烧成与未烧耐火材料;也可根据耐材化学成分不同分为:硅石耐材、铝硅酸盐耐材、镁质耐材、碳复合耐材等。
耐火材料使用工况的复杂及恶劣性决定了,依据使用环境不同需对耐火材料提出不同性能要求,包括其抗温度损害性能、抗热应力破坏性能及抗环境介质侵蚀性能等。
由于各耐火材料其理化性能存在较大差异,应结合反应器特点、工作环境及具体用途,选择适宜的耐火材料。对于流化床气化炉,内衬耐火材料的损坏主要分为化学侵蚀、热侵蚀、机械侵蚀三大类。化学侵蚀会导致耐火材料结构性能的降低,进而加大热力学侵蚀及机械侵蚀对材料耐磨性能的影响。
材料的选择需充分结合工艺特点。通常材料选取时需关注的理化指标包括耐压抗折强度、耐磨及热震稳定性、重烧线变率等。当反应工况下选择的材料、如浇注料未达所需烧结温度,则强度会大大降低,首先需要保证所选耐火材料在工作温度下具备较好的强度,或者在开始烘炉时烘至达到材质的烧结温度以保证工况运行时材料的强度较高。另外,耐火材料在制作施工、安装及烘炉过程中的不合理也会导致耐材的损坏。因此,必须确保厂家在施工制作过程中严格按照设计要求进行施工,同时保证整个过程满足耐材生产厂家提出的材料施工要求。确保材料中所含的水分完全转化为水蒸气逸出,避免炉子点火运行后因耐火材料中的水蒸气压力超过材料的拉伸强度进而引起衬里分层、崩溃、导致炉子内衬塌落。
2、流化床反应器及耐碱腐蚀耐材研究
2.1流化床反应器用耐火材料的现状
通常流化床用耐火材料内衬按作用可分为三类:耐磨材料;耐火材料;保温材料。现有流化床采用的耐火材料包括:磷酸盐耐材;碳化硅耐材;刚玉耐材;氮化硅结合碳化硅产品等。
磷酸盐砖适用于1200~1600℃温度范围,为500℃低温热处理得到的不烧砖,已在水泥窑应用多年,早期的循环流化床锅炉内衬也采用该材料。但在循环流化床锅炉的运行温度范围内(850~900℃),磷酸盐耐材性能不稳定,耐磨性差,但因价格优势,其早期在流化床具有较多应用。
碳化硅耐材具有优异的耐磨及热震稳定性。但对于煤气化工艺,因反应器内略带氧化性气氛导致其使用受限。报道指出,美国严禁在循环流化床锅炉中选用碳化硅耐材,且较高的成本也限制了碳化硅的使用。
硅酸铝质耐火材料(Al?O3-SiO?系),基本化学组成为Al?O3、SiO?。该系耐材中应用较多的为莫来石及刚玉耐火材料。莫来石因耐火度高、抗蠕变、抗化学侵蚀性好、荷重软化温度高、抗热震性能较好、体积稳定性能好以及电绝缘性强,成为理想的高级耐火材料。但是莫来石的化学成分不稳定,包括2Al?O3·SiO?及3Al?O3·2SiO?两种形式。刚玉耐火材料中,Al?O3含量高于90%且主晶相为α-Al?O3。
刚玉具有热力学强度高、化学稳定性好、抗热震性及抗磨损性好、抵抗还原剂作用能力强等性能,因此作为高级耐火材料的重要原料。
综合上述材料性能及价格等各方面因素考虑,煤气化炉通常选用刚玉作为内衬耐火材料,通常使用的品种有白刚玉、高铝刚玉和棕刚玉等。
对于煤气化炉,选取耐材组成及设计结构的不同导致耐材内衬的抗煤灰侵蚀能力各异。煤灰对耐火材料的侵蚀机理即煤灰矿物质与耐火材料反应、侵蚀的过程。研究表明,煤灰对高铝耐材的侵蚀最强,碳化硅耐材次之,刚玉耐火材料抗侵蚀能力最强。
2.2 不同耐火材料抗碱腐蚀特性研究
气化炉中各气氛腐蚀中,碱侵蚀对耐材内衬的破坏作用尤其强。炉内的碱金属蒸发、凝聚至耐火砖衬,尤其是缝隙处,在其中富集、渗透,导致砖衬腐蚀、开裂,耐材内衬遭受破坏。
目前,在碱金属对耐火材料的腐蚀方面,国内外开展了大量工作。高炉工作者制定了耐火材料抗碱性能试验方法国家标准,其以低气孔率高抗碱性为目标,研制了微气孔产品;徐国涛等通过考察碱金属对不同耐火材料的腐蚀性,研究耐火材料在不同条件下的碱侵蚀过程,并提出了耐材改进对策;李伟等在碳热还原条件下研究了硅铝系耐火材料的腐蚀行为,发现高铝砖的耐腐蚀性能最好,且碱金属的添加加剧了耐火材料的侵蚀,添加剂添加量增大侵蚀加剧;周世倬等研究了各种硅铝质耐材及碳素材料的抗碱侵蚀性能,发现碱金属对硅铝质耐材的侵蚀是由于形成了白榴石、钾霞石高体积膨胀物质等,从而导致了砖衬体积的膨胀,并得出刚玉质耐材的抗碱腐蚀性能最强;高峰等考察了含碱煤灰在不同耐火砖表面的润湿性及侵蚀性,发现刚玉砖受到的侵蚀最弱;Stjernberg等研究了莫来石/刚玉耐材与含碱材料的反应,发现碱金属与耐火砖反应生成了霞石及白榴石相,该些物相的生成导致砖内行程了一定的体积膨胀,进而加速了耐火材料的损毁。含碱物质会对铝含量高的耐火材料造成一定损害,从而导产生“碱裂解”。此外,含碱物质会形成粘结物进而损坏耐火材料,尤其易形成硫-碱化合物,损坏耐材的粘结结构。研究表明,900℃以下的碱蚀为耐火材料同含碱物质直接反应引发,而高温下的侵蚀则是因为将含钾化合物还原成生成了钾蒸汽,进而发生迁移氧化反应引起。
下面对含碱工况下常用耐火材料的抗碱腐蚀性进行详细介绍:
(1)硅铝系耐火材料
Al2O3-SiO2系耐火材料的基本化学组成是氧化铝和二氧化硅,依照氧化铝含量的高低。
采用Al2O3-SiO2系耐火材料,含碱化合物与之发生的化学反应如下:
A₃S₂+16SiO₂+3K₂O→3KAS₆(正长石)
A₃S₂+10SiO₂+3K₂O→3KAS₄(白榴石)
2A₃S₂+8SiO₂+6K₂O→6KAS₆(方钾霞石)
11Al₂O₃+K₂O+Na₂O→(K·Na)A11(β刚玉)
K₂SO₄·2CaSO₄+H₂0→2CaSO₄·K₂SO₄·H₂O(钾石膏)
2CaSO₄+K₂SO₄→2CaSO₄·K₂SO₄(无水钾石膏)
碱金属对Al2O3-SiO2质耐火材料的侵蚀是因为形成了白榴石、钾霞石、β-刚玉等,其的生成导致耐材内衬体积发生膨胀,最终导致了碱裂解现象的发生。反应产物取决于碱浓度和耐火材料中的Al2O3、SiO2的含量。碱金属对各种硅铝质耐火材料膨胀破坏的程度各不相同。
高铝砖(莫来石成分)的耐火材料最差,破损膨胀最为严重。碱金属同莫来石反应,在700~110℃生成霞石,含碱物相的生成会产生20%~25%的体积膨胀,导致材料损毁。
刚玉质耐火材料抗碱金属性能较好,体积变化最小。碱侵蚀的机理为:晶界物质与含碱材料发生反应产生了新物质,且该物质产生了一定的体积膨胀,导致刚玉耐材试块的碎裂,即一定温度、压力下K2O和Al2O3形成固溶体钾的过程,化学反应如下:
1/11K₂O(S)+Al₂O₃(S)→1/11(K₂O·Al₂O₃)(S)
另外,碱金属对耐火材料的腐蚀性能受具体反应温度、气氛、反应时间及碱金属存在形态的影响。不同气化工艺在选择气化炉内衬耐火材料时,应结合自身工艺特点及在气化炉内使用部位、具体反应工艺条件(气氛、温度等)、K形态等的不同而选取不同的耐火材料。但在高温和高碱金属浓度下,不存在绝对抗碱金属侵蚀的硅铝质耐火材料。因此,对于碱金属循环积累严重的高炉,下部不应采用高铝内衬,另外,气孔度是影响耐火材料抗碱金属性能的关键因素之一。
(2)含铬耐火材料
镁铬质、铬刚玉耐火材料耐火度高,高温强度大,抗热震性优良。由于其良好的抗碱性能及优良的耐高温特性,镁铬质耐火材料长期用作碱回收炉炉衬耐材。含铬耐火材料中Cr?O?,特别是基质中的Cr?O?有利于增大材料密度和热态结合强度,降低气孔率,改善抗渣侵蚀性。但是Cr?O?与铬矿在氧化气氛下易与碱金属氧化物(K?O、Na?O)反应生成低熔点的六价铬酸盐,其反应式如下:
2(Cr?O?)+O?+R?O→4(R?CrO?)(R-K、Na等)
该反应的发生,一方面不仅破坏了Cr?O?与铬矿的结构,而且形成的低熔物还会渗入砖内;另一方面铬酸盐R?CrO?是一种弱氧化性化合物,化学稳定性较高,六价铬是有毒的并能致癌,大量研究表明:人类的一些皮肤溃疡和呼吸道疾病均与Cr6+有关,且会对环境造成的污染具有持续性。随着环保意识的增强,已将处理“铬公害”提到了议事日程。
(3)铝酸钙系耐火材料
CaO-Al?O?二元系统中包括两个重要的化合物,即二铝酸钙、六铝酸钙。因良好的水硬化能力、脱碳能力及高温使用性能,在建材、冶金、国防等行业应用广泛。
六铝酸钙(CaAl??O??或CaO·6Al?O?,简写为CA?,矿物名称:黑铝钙石),因较佳的理化性能近年来倍受关注。其在CaO-Al?O?二元系统中,抗水化性最好、熔点(最高约1830℃分解熔融)。
CA?晶体各向异性生长,可形成六方片状晶体形貌,该晶型具有微孔结构,且在一定温度范围内能抑制烧结,保持材料的显气孔率基本不变,降低导热系数。值得一提的是,CA?与Al?O?具有极好的适配性,两者因平均热膨胀系数十分接近,可以进行任意配比而不会引起膨胀失配。同时,由于CA?熔点高,在高温还原性气氛下稳定性好,在碱性环境中具有较好的抗侵蚀能力。六铝酸钙材料发展前景优良。
在高温条件下,刚玉、CA?都会同K?O反应。刚玉与氧化钾反应生成β-刚玉,伴随着较大的体积膨胀,这是造成耐火内衬破坏的主要原因之一。但CA?的晶体结构与β-Al?O?晶体结构相似,将Ca2+嵌入层状氧化铝中,可在层间吸收碱金属离子,且体积不会发生明显变化;另外,CA?的体积密度(3.38g/cm?)与KA11的体积密度(3.37g/cm?)相近,所以当CA?被碱侵蚀时,与其它的耐火材料相比,其体积稳定性更高。
(4)镁铝尖晶石系耐火材料
镁铝尖晶石(MgO·Al?O?或MgAl?O?,简写为MA)是MgO-Al?O?二元系统中唯一稳定存在化合物。镁铝尖晶石为各向同性的八面体结构,Al-O、Mg-O间以离子键结合,其静电键强度相同,结构稳定。该种晶体结构保证了MA耐材优异的热震稳定性及耐磨性能,且在氧化还原性气氛下,对游离的SO?/SO?及K?O/Na?O具备较佳的抗侵蚀性,因此,MA在耐火材料行业应用广泛。另外,镁铝尖晶石熔点高(2135℃)、导热系数低、热膨胀系数小、强度高、硬度大、抗冲击、抗碱侵蚀能力强,且对铁的氧化物的作用也很稳定。
(5)复合材料
鉴于CA?及MA均具有较好的抗碱腐蚀性能,且CA?及MA的热膨胀系数相近、相容性好,可以任意比例配合,不存在膨胀失配问题。因此,可考虑将两种材料复合使用,目前已研制出CA?-MA复合轻质骨料,经研究表明其具有良好的热震稳定性、耐侵蚀性、耐磨性能及良好的抗渣侵蚀性。
(6)铝炭系耐火材料
铝炭系耐火材料在高炉上应用较多,如在存在碱蚀的铁水预处理炉、熔融还原炉都有着应用或潜在应用前景。其中SiAlON(碳化硅类)结合刚玉材质成为大型高炉上的关键耐火材料。在还原性气氛下,富含碱金属的高炉炉渣对SiAlON结合刚玉砖的侵蚀速度较小,其侵蚀机理为SiAlON与碱蒸气反应生成钾霞石,并参与了硅酸盐玻璃相的生成;刚玉颗粒与灰渣中的氧化亚铁、氧化钠和氧化钾等反应生成铁铝尖晶石及少量针状β-氧化铝。
但SiC在氧化性工况下使用,SiC氧化成SiO?,可生成碱硅酸盐,产生高温粘结相,与表面层反应同步,易形成挂渣层。这一方面可能会减缓碱蚀过程,但该高温粘结相的存在同时会粘附耐火材料及灰渣,可能进一步生成霞石及其他低温共熔物,造成基质脆化损毁。
3、流化床气化炉内衬耐材的建议
(1)结合流化床气化炉内工作介质温度高、腐蚀性强及内部物流对气化炉内衬冲刷严重的特点,气化炉衬里需具备耐冲刷、抗腐蚀、抗热震性能及一定的热体积稳定性。同时,今后煤气化炉耐火材料内衬的选取将更加偏重于其经济环保性,且要求施工方便、使用寿命更长、易修补等。
(2)工业规模气化炉选取适合的耐材内衬,需结合各自工艺特点及采用的原料特性,加强对其理化性能的关注,如耐压强度、抗折强度、耐磨性能、耐腐蚀性和热震稳定性等,该些性能是否达标,同样会影响气化炉的长周期稳定运行。建议建立相关检测标准,对耐火材料的性能进行全面检测,并请相关的专业技术人员和有实践经验的专家就相关检测进行评估,确保相关理化指标满足工艺设计要求;另外,所选生产施工厂家的资质及能力是否满足工艺要求也对气化炉耐火材料内衬的性能及使用寿命影响较大。
(3)气化炉应严格按照满足耐材使用性能要求的升降温曲线进行烘炉及降温处理,且在运行中尽量避免紧急停车,减少启停次数,避免耐材产生应力疲劳,导致内衬开裂。另外,需安排定期检修,发现开裂及时修补。
高炉炉缸的长寿对高炉长期稳定运行起着至关重要的作用,在高炉炉缸破损的诸多因素中,碱金属的侵蚀是一个重要的影响因素,这在国内外大量的高炉破损调查中已经得到了充分验证。在炉缸中,碱金属主要通过对炭砖等耐火材料进行渗透造成侵蚀,严重时在高炉内形成脆化层。为了选用抗碱性能好的耐火材料,必须选用一种方法对耐火材料进行评价,通过切实有效的数据进行对比分析。
目前对于耐火材料抗碱性测定的方法,中钢集团耐火材料研究院等起草了GB/T 14983—2008国家标准,即《耐火材料抗碱性实验方法》。它是从耐火砖内切出20mm左右大小的立方体,对各个面进行打磨并用游标卡尺测量尺寸,然后将木炭、碳酸钾和试样放入坩埚中,通过坩埚盖进行连接,往炉内通入氮气后升温到1100℃保温30h,实验结束后观察耐火砖的宏观形貌和微观形貌,测定耐火砖的抗压强度变化率。但是该方法存在以下缺点:(1)国标中的试验方法是通过碱蒸气与耐火材料的反应评价耐火材料的抗碱金属性能,但是通过热力学分析可知,在高炉炉缸中,碱蒸气并不会直接和耐火材料发生反应,而是扩散到耐火材料内部后被液化后才能与耐火材料反应形成新相,国标的方法与高炉内实际情况严重不符;(2)实验结束后,国标中仅仅从宏观形貌、微观形貌、抗压强度变化率进行表征,表征手段太少,不能够综合评价耐火材料抗碱性的优劣,应该增加质量变化率、体积变化率,EDS分析等手段来全面评价耐火材料抗碱性能优劣。
以往的观点认为高炉内碱金属对耐火材料的侵蚀是通过碱金属气体与耐火材料反应进行的,因此我们对K蒸气与炭砖的反应进行了热力学分析。炉内K蒸气在炉内反应K2O、K2CO3
蒸气在炉内反应K2O、K2CO3。ΔG2=-213800+152.16T+RTln(1/((Pk/Pθ)2×(Pco/Pθ)3),当T=750℃时,上式反应的临界K蒸气分压为52.7KPa和16.2KPa,这在实际高炉中是不可能发生的,因此K蒸气不会直接与耐火材料反应破坏耐火材料。根据克劳佩龙-克劳修斯方程计算钾蒸气在高压条件下的液化条件,可知钾蒸气在炉缸高压条件下,可在低于932℃的条件下液化。由此我们再对液态钾与耐火材料的反应进行热力学分析,温度为750℃时,对于液态钾与耐火材料生成白榴石、钾霞石等的反应,它们的ΔG<0,表明该反应可以发生。因此可以得出结论,碱金属在炉内被还原形成碱金属蒸气,碱蒸气不会直接和耐火材料发生反应,而是通过缝隙渗入砖衬,在高炉炉缸冷却的作用下,碱蒸气开始液化并不断富集,然后与CO等物质形成新相后开始膨胀。